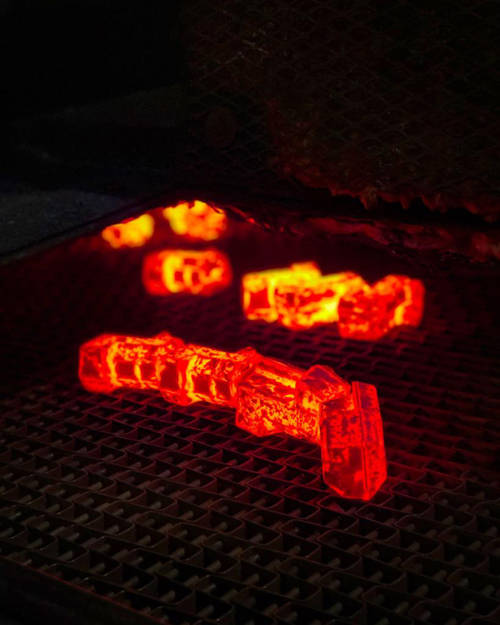
Both hot and cold forged products are stronger than metal castings. Forged parts have more predictable strength and integrity and typically exhibit more uniform and superior physical properties than castings.
During the forging process, internal metal defects that may occur in the ingot are refined or eliminated. This is due to the forced flow of material grains in a specific direction caused by forging, which is not present in continuously cast bars. Forgings are usually pretreated to orient the grains in a specific direction to obtain maximum metal strength and ductility.
In addition, manufacturers of metal forgings can produce parts more economically, resulting in cost savings for their customers. And, because metal forgings are more ductile, the products are more durable, stronger and easier to shape, making forged products perfect for heavy-duty service.
During processing, casting requires very close attention to the melting and cooling stages to prevent alloy segregation. Forgings respond better to heat treatment, resulting in a more uniform thermal response, giving the final product greater straightness and dimensional accuracy.