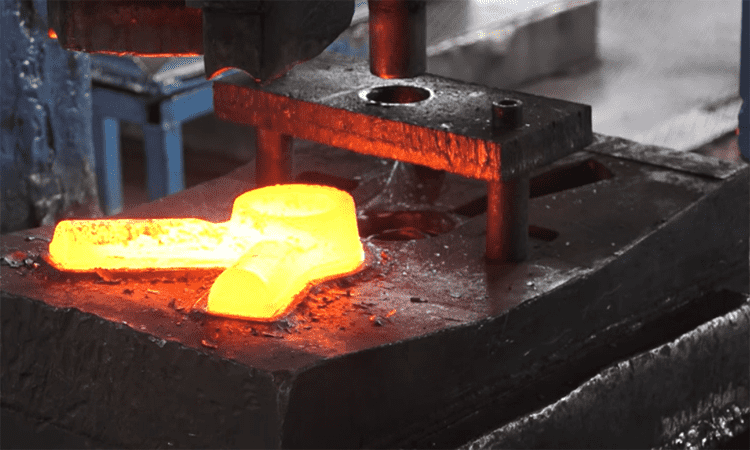
Aluminum in its elemental form is a fairly soft and lightweight metal that is often alloyed with copper, magnesium, tin or zinc to increase its strength, durability, quality and workability. Approximately 85% of aluminum parts are made from forging. Aluminum alloys are easily forged. Due to their low melting points, cast aluminum products are relatively inexpensive, but they have lower tensile strengths. Common forged aluminum alloys include 6061, 6063, 6082, 7075, etc. Aluminum alloys are widely used in engineering applications and components that require light weight and corrosion resistance. Forged aluminum parts are used in aerospace projects, automotive engine components, shipbuilding and other salt water sensitive applications.
After learning about hot and cold forging methods, many people may still wonder about the choice of forging methods for aluminum parts. In general, cold forging is only chosen when the aluminum part is simple and regular in shape. Due to the high cost of cold forging dies, the requirement for order quantity is also high, usually above 30,000 pieces. For irregular aluminum parts, hot forging is recommended and most of the forged aluminum parts will be further processed to get finished parts. Both hot forged and cold forged aluminum parts can be heat treated and anodized when necessary.